Décision d'exécution (UE) n° 2022/2110 du 11/10/22 établissant les conclusions sur les meilleures techniques disponibles (MTD), au titre de la directive 2010/75/UE du Parlement européen et du Conseil relative aux émissions industrielles, dans les industries de transformation des métaux ferreux
(JOUE n° L 284 du 4 novembre 2022)
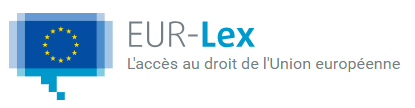
Consulter le texte sur EUR-Lex